What Is the Difference Between QC and QA in Sports Pain Patches OEM? A Complete Guide for Brands
As the demand for Custom Sports Pain Patches and Private Label Sports Pain Patches continues to rise, brands must prioritize quality in every step of the production process. Two key pillars that uphold product integrity are Quality Control (QC) and Quality Assurance (QA). Though these terms are often used interchangeably, they serve very different functions.
In this article, we’ll explore the difference between QC and QA in the context of Sports Pain Patches OEM manufacturing. We'll explain how both processes are essential to producing safe, effective, and compliant pain relief products—and how choosing the right Sports Pain Patches Manufacturer or Sports Pain Patches Supplier can protect your brand’s reputation and satisfy consumer expectations.
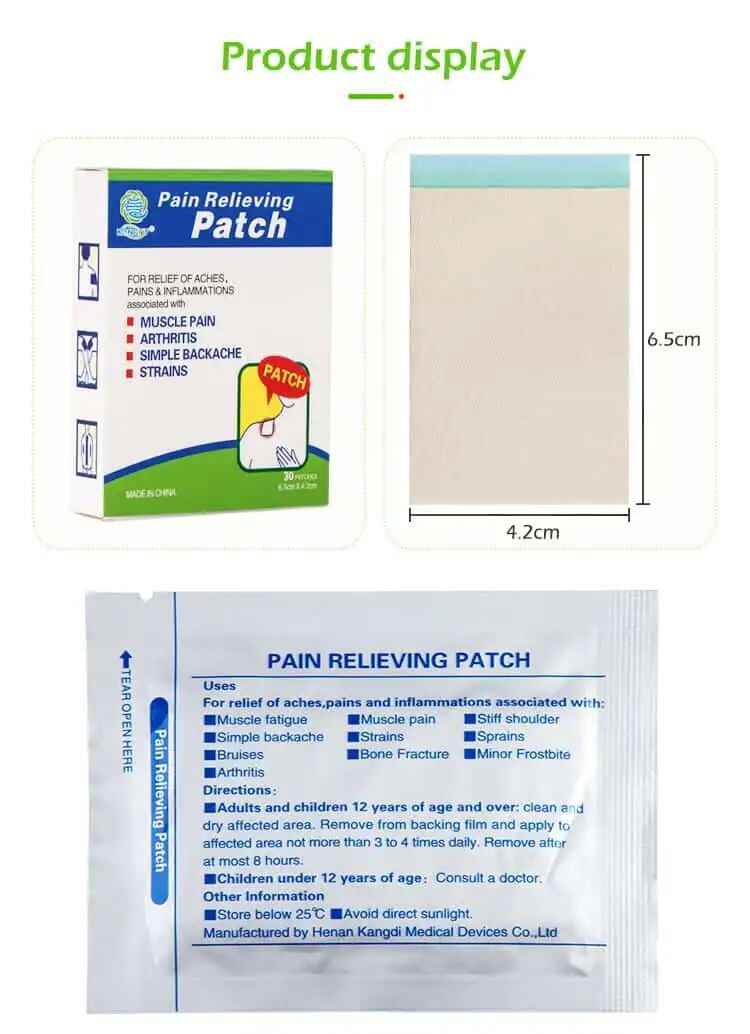
1. Understanding the Basics: QC vs. QA
Aspect | Quality Assurance (QA) | Quality Control (QC) |
---|---|---|
Focus | Process-oriented | Product-oriented |
Goal | Prevent defects | Identify defects |
Timing | Before production | During/after production |
Responsibility | Everyone involved in production | Specific QC team |
Activities | SOPs, training, audits | Testing, inspection, batch review |
2. What Is Quality Assurance (QA) in Sports Pain Patches OEM?
Quality Assurance is a proactive, process-based approach designed to prevent errors and ensure that every Custom Sports Pain Patch is manufactured under strict compliance with industry standards.
Key Functions of QA in a Sports Pain Patches OEM:
A. Establishing Standard Operating Procedures (SOPs)
QA teams develop and maintain clear guidelines for every step of production—from sourcing raw materials to final packaging. A reliable Sports Pain Patches Manufacturer will have SOPs aligned with:
GMP (Good Manufacturing Practices)
ISO 13485 (for medical devices)
FDA regulations
B. Supplier Qualification
QA teams verify that all Sports Pain Patches Suppliers (e.g., for adhesives, herbal extracts, packaging materials) meet safety and quality requirements before any ingredient or component is used.
C. Document Control
QA ensures all documents (e.g., batch records, safety reports, certificates of analysis) are accurately maintained for traceability and regulatory audits.
D. Employee Training
QA is responsible for ensuring that personnel are trained in hygiene, equipment handling, and production protocols to avoid human error.
3. What Is Quality Control (QC) in Sports Pain Patches Manufacturing?
Quality Control is a reactive, product-focused strategy. It involves the detection and correction of defects during or after the manufacturing process of Private Label Sports Pain Patches.
Key Functions of QC in a Sports Pain Patches Manufacturer:
A. Raw Material Inspection
Before production, QC teams test incoming ingredients and materials for purity, potency, and compliance with specifications. For example:
Menthol concentration levels
Fabric thickness and tensile strength
Adhesive uniformity
B. In-Process Monitoring
During production, QC inspectors assess:
Patch dimensions and weight
Uniformity of active ingredient distribution
Adhesive application precision
C. Finished Product Testing
After manufacturing, QC tests the Custom Sports Pain Patches for:
Active ingredient dosage (e.g., 5% menthol)
Skin safety (dermatological patch test)
Adhesion performance (stickiness over time)
Packaging integrity (leak-proof, tamper-evident)
D. Batch Release Control
A product batch is only released after it passes all quality checkpoints. If there’s any failure, the batch is either reprocessed or discarded.
4. Why Are Both QA and QC Important in Sports Pain Patches OEM?
A. Safety and Compliance
A reliable Sports Pain Patches OEM ensures that both QA and QC are integrated into their system. This dual approach:
Minimizes risk of recalls
Meets health authority requirements (e.g., FDA, CE, Health Canada)
B. Consistency in Custom Sports Pain Patches
Consumers expect reliable results. QA ensures the process is standardized, while QC ensures the end product consistently meets those standards.
C. Reputation and Brand Trust
If you're launching Private Label Sports Pain Patches, any safety issue can tarnish your brand. A Sports Pain Patches Supplier that offers robust QA/QC systems protects your reputation.
D. Cost Efficiency
Detecting defects early (QC) and preventing them through solid procedures (QA) helps avoid costly product failures and legal liabilities.
5. What to Look for in a Quality-Focused Sports Pain Patches Manufacturer
If you're sourcing an OEM partner to develop your Custom Sports Pain Patches, ask these questions to evaluate their QA and QC systems:
✅ Do they have GMP and ISO certifications?
These credentials confirm that their QA protocols align with international quality benchmarks.
✅ Can they share SOP samples?
A professional Sports Pain Patches Supplier should be transparent about their process controls.
✅ What kind of testing do they perform?
Ask for specifics on ingredient testing, patch adhesion, skin safety, and packaging durability.
✅ Do they provide batch test reports?
Your Sports Pain Patches Manufacturer should provide Certificates of Analysis (COA) with every order.
✅ How do they handle product recalls or complaints?
A proper QA system includes a documented method for handling defective products and tracing the root cause.
6. Real-World Example: QA vs. QC in Action
Scenario: You order a batch of Private Label Sports Pain Patches infused with menthol and camphor from a Sports Pain Patches OEM.
QA’s Role: The OEM ensures the SOPs are followed—from weighing ingredients to sealing packages. They also verify that the personnel handling raw materials wear gloves and masks to avoid contamination.
QC’s Role: Midway through production, the QC team notices a deviation in menthol concentration. They halt the batch and investigate. Later, the finished patches undergo adhesion and safety testing before being cleared for shipping.
Thanks to this QA/QC collaboration, your brand receives safe and effective pain patches—without any issues reaching your customers.
7. Conclusion: Choose a Sports Pain Patches Supplier Who Prioritizes Both QA and QC
When entering the pain relief product market, partnering with a Sports Pain Patches Manufacturer that emphasizes both QA and QC isn’t just a good idea—it’s essential.
From ingredient inspection to SOPs and final product testing, these two systems work hand-in-hand to guarantee that your Custom Sports Pain Patches are:
Safe for consumers
Consistent in quality
Compliant with regulations
Trustworthy under your private label
Always choose a Sports Pain Patches OEM who can demonstrate excellence in both Quality Assurance and Quality Control.
Frequently Asked Questions (FAQs)
1. What does a Sports Pain Patches OEM do in terms of QA and QC?
A Sports Pain Patches OEM designs, manufactures, and tests products using rigorous QA (process oversight) and QC (product inspection) to ensure compliance, safety, and effectiveness.
2. Can I request documentation of QA/QC processes from a Sports Pain Patches Manufacturer?
Yes, reputable manufacturers should provide SOPs, GMP certifications, COAs, and quality testing reports upon request.
3. How does QC prevent faulty Custom Sports Pain Patches from reaching the market?
QC tests raw materials, monitors in-process production, and examines final products to detect defects. If issues are found, the affected batch is either corrected or rejected.
4. Why is QA important in Private Label Sports Pain Patches?
QA builds a foundation of reliable procedures, ensuring every product you label and sell meets consistent safety and quality standards.
5. Do Sports Pain Patches Suppliers offer customized QA protocols?
Yes, high-end suppliers can tailor QA programs based on your product's complexity, target market regulations, and branding needs.
Ready to launch a high-quality private label product? Partner with a certified Sports Pain Patches OEM that values both QA and QC—and bring safe, effective pain relief to your customers.