What Testing is Required for Custom Heat Therapy Patches?
Custom heat therapy patches have gained widespread popularity for their ability to provide relief from chronic pain, muscle aches, and other discomforts. However, to ensure that these patches are safe, effective, and reliable, rigorous testing is required throughout the manufacturing process. Whether you are working with a Heat Therapy Patch Manufacturer, Heat Therapy Patch OEM, or offering a Custom Heat Therapy Patch under a Private Label Heat Therapy Patch brand, the testing process ensures that your product meets regulatory standards and performs as expected. This article will explore the various types of testing required for custom heat therapy patches and why they are crucial for product success.
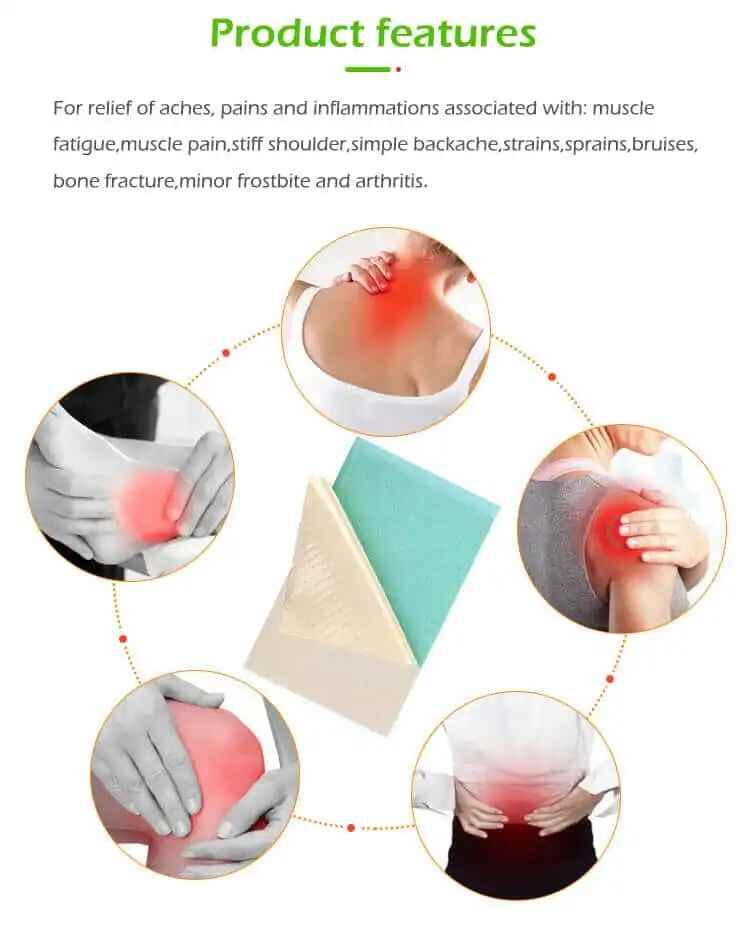
1. Safety Testing
The primary concern for any health-related product, including Custom Heat Therapy Patches, is the safety of its users. Because heat therapy patches are applied directly to the skin, safety testing is critical to prevent skin irritation, burns, or allergic reactions. Several tests must be conducted to ensure the patch is safe for use by the target consumer.
Dermal Irritation Testing
This test evaluates whether the Heat Therapy Patch causes any irritation to the skin after prolonged contact. A patch is applied to the skin for a specific duration, and dermatologists monitor for redness, swelling, or other signs of irritation. This test is particularly important for consumers with sensitive skin.
Dermal Sensitization Testing
To check for potential allergic reactions, Heat Therapy Patch Manufacturers conduct dermal sensitization testing. The patch is applied to a small area of the skin over multiple sessions to identify if any allergic response occurs. This test helps ensure that the patch will not cause rashes or long-term skin issues for users.
Patch Adhesion Testing
Since the Custom Heat Therapy Patch needs to stay securely in place during use, adhesion testing is crucial. This test examines the strength and longevity of the adhesive used in the patch. The goal is to ensure that the patch will not peel off prematurely or cause discomfort while still being easy to remove without leaving residue.
2. Performance Testing
Heat Therapy Patch Suppliers need to ensure that their products deliver consistent and effective heat therapy. Performance testing focuses on the heat release and the duration for which the patch remains effective. The following tests are essential to guarantee the desired therapeutic effect.
Heat Release Rate Testing
This test evaluates how much heat the Heat Therapy Patch generates and how evenly the heat is distributed across the patch. The patch is monitored to ensure that it provides a consistent level of heat over the intended period. A patch that generates too little heat will fail to provide the expected pain relief, while excessive heat could cause burns.
Duration of Heat Testing
To confirm that the Custom Heat Therapy Patch provides long-lasting relief, manufacturers conduct duration of heat testing. This test measures how long the patch continues to deliver heat after it is applied to the skin. The patch must maintain the desired temperature for the full recommended duration to be considered effective.
Temperature Control Testing
For Private Label Heat Therapy Patch products, it is essential to control the temperature within safe and effective limits. Temperature control testing ensures that the patch does not overheat, which could lead to burns or other injuries. It also guarantees that the patch’s heat remains at a therapeutic level for the entire duration of use.
3. Material Testing
The materials used in Custom Heat Therapy Patches play a significant role in the product's overall performance and safety. Testing the materials ensures that they are safe, durable, and capable of delivering the intended benefits.
Material Compatibility Testing
Before a Heat Therapy Patch OEM can produce patches on a large scale, it is essential to test the materials for compatibility. The adhesive, heat-producing ingredients, and the backing material must work together without compromising the product’s safety, comfort, or effectiveness.
Hypoallergenic Testing
Because consumers have varying sensitivities, it is important to test the materials used in Heat Therapy Patches for hypoallergenic properties. Ensuring that the patch does not contain substances known to trigger allergic reactions, such as certain fragrances or latex, is essential for preventing harm to consumers.
Durability Testing
Durability testing checks how well the materials in the Custom Heat Therapy Patch withstand external factors such as moisture, temperature variations, and physical stress. Patches need to maintain their integrity during use, even in challenging conditions. Durability testing helps determine the shelf life of the product as well.
4. Regulatory Compliance Testing
For any Heat Therapy Patch Manufacturer, it is important to ensure that the product complies with relevant regulations. Regulatory testing ensures that the patch meets the required legal standards for sale in various markets, including the U.S., Europe, and other regions.
FDA Compliance Testing
In the United States, the Food and Drug Administration (FDA) oversees the safety and effectiveness of products intended for therapeutic use. While heat therapy patches may not be classified as medical devices in all cases, those making medical claims or intended for therapeutic use may need to meet FDA requirements. This can include pre-market approval or compliance with the FDA's Good Manufacturing Practices (GMP).
ISO Certification
Internationally, Heat Therapy Patch Suppliers may seek ISO certification to ensure that their products meet global safety and quality standards. ISO 13485 is a common certification for medical devices, and it can apply to patches that make therapeutic claims.
5. Environmental Testing
Environmental factors can affect the performance and safety of Heat Therapy Patches. Environmental testing ensures that the patch maintains its integrity under various conditions. This is especially important for patches that are used in diverse climates and environments.
Storage and Stability Testing
This test evaluates how the Heat Therapy Patch performs under different storage conditions, such as changes in temperature, humidity, and exposure to light. The patch must maintain its heat-producing capabilities and adhesive properties throughout its shelf life.
Heat and Cold Resistance Testing
Because Custom Heat Therapy Patches may be used in varying environments, they must be tested for heat and cold resistance. This ensures that the patch works effectively in both hot and cold climates, maintaining its effectiveness regardless of external temperature fluctuations.
6. User Experience Testing
User experience (UX) testing is a critical aspect of ensuring that Heat Therapy Patches meet consumer expectations in terms of comfort, usability, and overall satisfaction.
Comfort and Fit Testing
Comfort testing assesses how well the Heat Therapy Patch adheres to the skin, its flexibility, and how comfortable it is to wear for extended periods. A well-designed patch should be thin, breathable, and flexible, allowing users to move freely while wearing it.
Ease of Application and Removal Testing
For any Private Label Heat Therapy Patch, the ease with which the patch can be applied and removed is a key factor. Testing ensures that the patch is easy for consumers to apply to the skin without difficulty and can be removed without causing discomfort or leaving residue.
Conclusion
In conclusion, rigorous testing is essential for the development and production of Custom Heat Therapy Patches. From safety and performance to material testing and regulatory compliance, each stage of testing ensures that the patch is safe, effective, and reliable for consumers. Whether you're working with a Heat Therapy Patch Manufacturer, a Heat Therapy Patch OEM, or offering a Private Label Heat Therapy Patch, these tests are crucial for building consumer trust and ensuring product success. Investing in comprehensive testing not only guarantees a high-quality product but also helps protect your brand’s reputation and compliance with regulatory standards.
Frequently Asked Questions
1. What types of testing are required for Heat Therapy Patches?
The main types of testing include safety testing (dermal irritation and sensitization), performance testing (heat release and duration), material testing (hypoallergenic and durability), regulatory compliance testing (FDA and ISO certification), and user experience testing (comfort and ease of use).
2. Why is heat release testing important for Custom Heat Therapy Patches?
Heat release testing ensures that the patch generates the right amount of heat for effective pain relief without exceeding safe limits.
3. How can Private Label Heat Therapy Patch products benefit from rigorous testing?
Rigorous testing helps ensure that the patches meet safety, performance, and regulatory standards, building consumer trust and enhancing brand reputation.
4. What is the role of durability testing in Custom Heat Therapy Patch production?
Durability testing ensures that the patch remains effective and intact under varying environmental conditions, which is crucial for long-term shelf life and consumer satisfaction.
5. How can environmental testing impact Heat Therapy Patch Manufacturers?
Environmental testing ensures that the patches maintain their functionality under different conditions, such as heat, cold, humidity, and exposure to light, providing reliable performance regardless of the environment.