The Importance of Quality Control in OEM Herbal Pain Patches for B2B Clients
In today’s highly competitive health and wellness market, businesses looking to provide effective pain relief solutions must focus on offering high-quality products to meet consumer demand. For B2B clients, partnering with a reliable Herbal Pain Patches Manufacturer that prioritizes quality control is essential. This article delves into why quality control is paramount when dealing with Herbal Pain Patches OEM, Custom Herbal Pain Patches, and Private Label Herbal Pain Patches, and how it impacts both the product’s efficacy and the long-term success of the business.
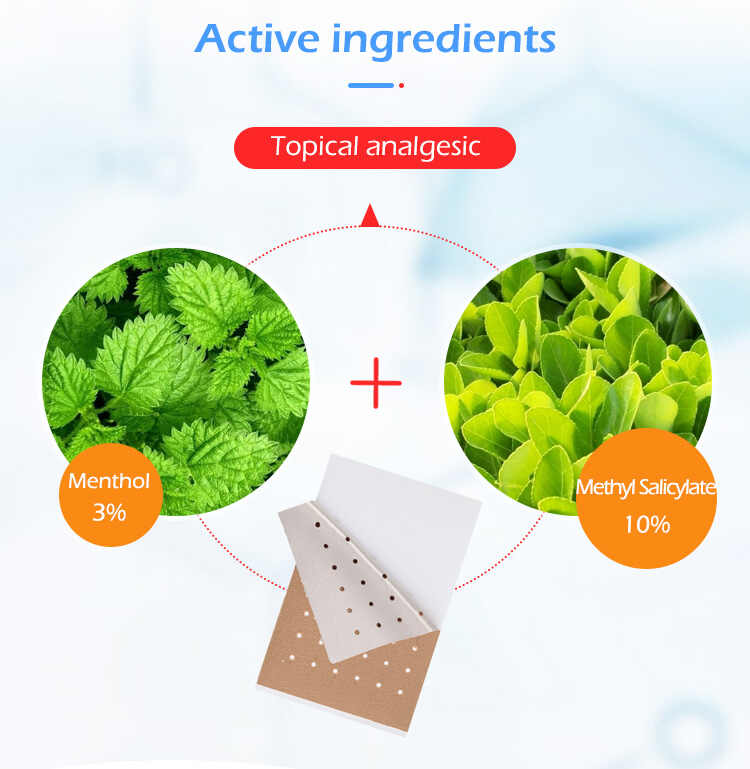
Why Quality Control Matters in Herbal Pain Patch Manufacturing
Quality control is a crucial component of the Herbal Pain Patches OEM process. Whether you're a small start-up or a well-established brand, maintaining consistency in product quality is essential to ensure customer satisfaction, regulatory compliance, and a reputable market presence. Here are several reasons why robust quality control is necessary:
1. Ensuring Product Efficacy
At the core of any pain relief product, especially Custom Herbal Pain Patches, is its ability to provide effective relief. Subpar manufacturing practices can result in inconsistencies in the concentration of active ingredients, leading to ineffective products that fail to alleviate pain as promised. High-quality Herbal Pain Patches Manufacturers rigorously test and measure each batch, ensuring that the right amount of active herbal ingredients, like menthol or camphor, are infused into every patch.
2. Compliance with Industry Regulations
The health and wellness sector is highly regulated, and Herbal Pain Patches OEM suppliers must adhere to stringent guidelines set by organizations like the FDA, CE, or other national health authorities. Poor quality control can result in the violation of these regulations, potentially leading to product recalls, fines, or even legal actions. Manufacturers with strong quality control systems ensure their products meet both local and international standards, making them a safer choice for B2B clients looking to build a reliable brand.
3. Brand Reputation and Trust
For Private Label Herbal Pain Patches brands, trust is a significant factor in consumer decisions. If the product consistently fails to work, it reflects poorly on the brand, regardless of the manufacturer’s name. By investing in quality control, B2B clients can guarantee that the product performs as expected, ensuring that customers remain loyal to the brand. Positive reviews and word-of-mouth recommendations are essential for business growth, and quality control plays a direct role in maintaining a strong reputation.
4. Cost Reduction
At first glance, robust quality control might seem like an additional expense, but in the long run, it can save a company substantial amounts of money. Poorly manufactured patches may lead to customer complaints, returns, and wasted inventory. Additionally, products that do not meet quality standards might require further testing, reprocessing, or even disposal. Investing in quality control ensures that the final product is reliable, reducing the chance of costly recalls and customer dissatisfaction.
Key Elements of Quality Control in Herbal Pain Patch Manufacturing
To understand the full importance of quality control in Herbal Pain Patches OEM production, it’s essential to look at the specific measures that contribute to high product quality:
1. Ingredient Sourcing and Testing
The quality of the herbal ingredients used in the patches is critical. Reputable Herbal Pain Patches Suppliers source ingredients from certified and reliable suppliers. These ingredients undergo rigorous testing for purity, potency, and safety before being incorporated into the patches. Inadequate testing or sourcing inferior ingredients could result in a product that not only underperforms but also poses health risks to consumers.
2. Manufacturing Process Monitoring
During the production of Custom Herbal Pain Patches, every step of the process must be carefully monitored. From the extraction and blending of active herbal ingredients to the formulation of the adhesive layer, each phase must meet strict standards. Modern manufacturers employ automated systems to control temperature, humidity, and timing, ensuring consistency and precision. Inconsistent production methods can result in patches that are too potent, too weak, or cause adverse skin reactions.
3. Packaging Integrity
Packaging plays a significant role in the overall quality of the product. Not only must the packaging ensure the integrity and shelf life of the Herbal Pain Patches, but it also needs to comply with labeling regulations. A well-designed packaging process, with tamper-proof seals and clear instructions, can help protect the product from contamination and degradation. Additionally, clear labeling ensures that customers are well-informed about the ingredients and usage instructions, reducing potential misuse.
4. Batch Testing and Inspection
Batch testing involves analyzing samples from each production lot to confirm that every batch of Herbal Pain Patches OEM meets the required standards for safety and efficacy. This may involve chemical analysis to ensure that the active ingredients are within the correct concentration levels and dermatological testing to confirm that the patch will not cause irritation. Manufacturers should also conduct physical inspections of the patches, checking for defects such as improper adhesive strength or uneven distribution of ingredients.
Benefits of Implementing Strong Quality Control in Herbal Pain Patches OEM
1. Improved Customer Satisfaction
Quality control ensures that every product meets customer expectations. When B2B clients offer reliable, high-quality Private Label Herbal Pain Patches, they’re more likely to build strong relationships with consumers, leading to repeat business and positive reviews. High customer satisfaction fosters brand loyalty, which is invaluable in the competitive wellness market.
2. Competitive Advantage
A company that consistently delivers high-quality, effective pain relief patches has a distinct competitive edge in the marketplace. By collaborating with a trusted Herbal Pain Patches Manufacturer that implements effective quality control, B2B clients can stand out in a crowded market and attract customers who value reliability and effectiveness in their pain management solutions.
3. Fewer Returns and Complaints
Poor product quality can lead to high return rates, which negatively impacts profitability. By ensuring rigorous quality control, businesses can reduce the likelihood of complaints and returns, making the entire sales process smoother and more cost-effective.
4. Long-Term Cost Savings
While the initial investment in quality control systems might seem substantial, it ultimately saves money by reducing waste, recalls, and customer compensation. Over time, companies that prioritize quality can achieve a higher return on investment and increased profitability due to enhanced customer retention and fewer operational disruptions.
Conclusion
For B2B clients looking to provide Custom Herbal Pain Patches or Private Label Herbal Pain Patches, partnering with a reliable Herbal Pain Patches Supplier that places a premium on quality control is essential. By ensuring that each batch of patches meets the highest standards, companies can offer safe, effective, and reliable pain relief solutions that satisfy customers and foster business growth. Quality control is not just a regulatory requirement—it’s a key to sustained success in a competitive market.
Frequently Asked Questions
Q1: How does quality control impact the efficacy of Herbal Pain Patches?Quality control ensures that the correct concentration of active ingredients is included in each patch, guaranteeing its effectiveness in relieving pain.
Q2: What are the risks of poor quality control in Herbal Pain Patch manufacturing?Poor quality control can lead to ineffective products, adverse skin reactions, and non-compliance with regulatory standards, which can damage a brand’s reputation and lead to costly recalls.
Q3: Why should B2B clients invest in quality control when sourcing Herbal Pain Patches OEM?Investing in quality control ensures that the product is safe, effective, and consistent, which is crucial for maintaining customer trust and brand integrity.
Q4: How can batch testing improve the quality of Herbal Pain Patches?Batch testing verifies that each production lot meets safety, efficacy, and quality standards, helping to prevent defective patches from reaching consumers.
Q5: What are the benefits of partnering with a certified Herbal Pain Patches Manufacturer?A certified manufacturer adheres to industry standards, ensuring the production of high-quality, compliant, and effective herbal pain relief patches.