Regulations and Compliance Requirements in Medical Cold Therapy Patches OEM Collaboration
When partnering with a Cold Therapy Patches Manufacturer for your medical product line, understanding regulatory and compliance requirements is crucial. In the world of Cold Therapy Patches OEM, overlooking even minor legal or quality standards can lead to costly recalls, reputational damage, or even regulatory sanctions. Whether you are creating Custom Cold Therapy Patches or launching Private Label Cold Therapy Patches, aligning with a knowledgeable Cold Therapy Patches Supplier ensures your products meet global standards and succeed in competitive markets.
This article dives deeply into the essential regulations and compliance requirements brands must understand when working with an OEM partner for medical cold therapy patches.
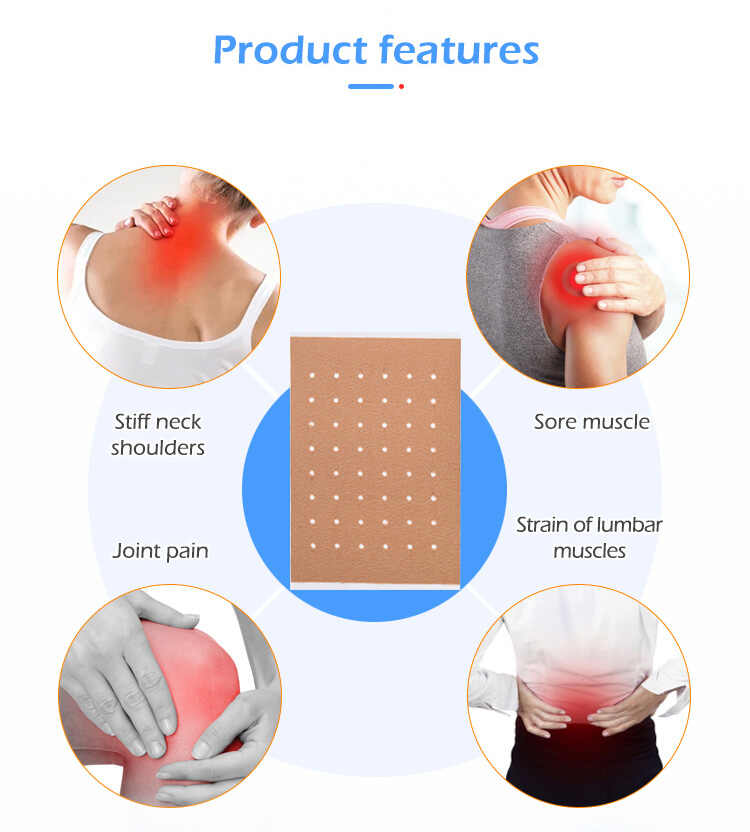
Why Compliance Is Critical in Medical Cold Therapy Patches Manufacturing
Medical devices—including cold therapy patches that claim therapeutic effects—are subject to strict global regulations to ensure safety, efficacy, and consumer protection. A reliable Cold Therapy Patches OEM must adhere to these standards at every stage: design, production, testing, labeling, and distribution.
Compliance guarantees:
Patient safety
Market access across different regions
Lower risk of recalls and lawsuits
Higher brand credibility
Successful audits and inspections
Choosing a Cold Therapy Patches Manufacturer that understands these complexities is not optional—it's a critical success factor.
Key Regulations and Standards in Cold Therapy Patches OEM Collaboration
1. FDA Regulations (United States)
In the U.S., cold therapy patches that relieve pain or treat injuries are considered Class I or Class II medical devices depending on claims and ingredients.
Key requirements include:
510(k) Clearance: If the product is substantially equivalent to an existing device, a 510(k) premarket notification is needed.
Good Manufacturing Practices (GMP): Under the FDA's 21 CFR Part 820, manufacturers must implement quality systems.
Labeling Compliance: Claims must be scientifically backed and labeling must include proper usage, warnings, and storage instructions.
Registration and Listing: The Cold Therapy Patches Manufacturer must be registered with the FDA and list all marketed devices.
Partnering with a Cold Therapy Patches OEM that has 510(k) experience can significantly reduce time to market.
2. CE Marking (European Union)
For brands targeting the European Economic Area (EEA), CE marking is mandatory.
Key steps include:
Medical Device Regulation (MDR) Compliance: Cold therapy patches now fall under stricter rules post-2021.
Risk Classification: Most cold therapy patches are Class I, but additional functions (e.g., embedded medicines) could elevate classification.
Technical Documentation: Detailed files about the product’s design, manufacturing process, and risk assessments are required.
Notified Body Involvement: Higher-class devices need third-party evaluation.
Your Cold Therapy Patches Supplier must support the creation of technical documentation and clinical evaluations.
3. ISO 13485 Certification
ISO 13485 is the global standard for quality management systems in medical devices.
A certified Cold Therapy Patches Manufacturer ensures:
Consistent product quality
Risk management integration
Full traceability of production and materials
Regular auditing and continuous improvement
Only collaborate with a Cold Therapy Patches OEM that holds valid ISO 13485 certification to safeguard your brand.
4. Other Global Regulations
Health Canada: Requires a Medical Device License (MDL) for cold therapy patches classified as medical devices.
TGA Australia: Conformity assessment processes for cold therapy patches under the Australian Register of Therapeutic Goods (ARTG).
Japan PMDA: Stringent pre-market approvals and on-site inspections.
A knowledgeable Cold Therapy Patches Supplier can advise you on multi-region compliance strategies if you're targeting global distribution.
Compliance Requirements Throughout the OEM Process
Design Phase
Risk Analysis: Identify potential safety issues early.
Intended Use Statements: Precisely define therapeutic claims to avoid overstepping regulatory bounds.
Human Factors Testing: Ensure ease of use to minimize misuse risks.
Material Selection
Biocompatibility Testing: Raw materials must not cause irritation, allergic reactions, or cytotoxicity.
Ingredient Disclosure: Full transparency for any cooling agents (e.g., menthol, camphor).
Manufacturing Process
Controlled Environments: Many Custom Cold Therapy Patches require production in controlled cleanrooms.
Documented Procedures: SOPs (Standard Operating Procedures) for every production step.
Validation Processes: Each critical process (e.g., adhesive application) must be validated.
Labeling and Packaging
Unique Device Identifier (UDI): Required in markets like the U.S. and EU for traceability.
Multilingual Instructions: Mandatory for products sold across different countries.
Proper Storage Instructions: Cold therapy patches must specify storage conditions to maintain efficacy.
Post-Market Surveillance
Complaint Handling Systems: Required to track and respond to customer issues.
Adverse Event Reporting: Mandatory reporting of significant issues to regulatory bodies.
Periodic Safety Update Reports (PSURs): Needed in some jurisdictions for continuous risk assessment.
How to Choose a Compliant Cold Therapy Patches OEM Partner
When selecting a Cold Therapy Patches Manufacturer, verify:
Certification and Audit History: ISO 13485, FDA inspections, CE audits
Regulatory Experience: Proven success with 510(k), MDR, TGA, etc.
Transparent Documentation: Clear access to quality system documentation and production records.
Proactive Communication: Alerts on any regulatory changes that may impact your products.
Flexible Customization Options: Especially critical for Custom Cold Therapy Patches and Private Label Cold Therapy Patches.
Remember, a compliant Cold Therapy Patches Supplier is not just a vendor—they are a strategic partner in your brand's success.
Related Questions and Answers
Q1: Do all Cold Therapy Patches require FDA approval?
A1: Not all patches require full FDA approval; many need only 510(k) clearance if deemed substantially equivalent to existing products.
Q2: Can I sell Private Label Cold Therapy Patches in Europe without CE marking?
A2: No, CE marking is mandatory for medical devices sold in the European Union, even if privately labeled.
Q3: What is ISO 13485 and why is it important in Cold Therapy Patches OEM?
A3: ISO 13485 is the international standard for medical device quality management systems; it ensures that the manufacturer consistently meets regulatory and customer requirements.
Q4: How can a Cold Therapy Patches Supplier help with regulatory compliance?
A4: A qualified supplier offers technical documentation, risk management support, and guidance through certifications and audits.
Q5: What happens if my Cold Therapy Patches do not meet compliance standards?
A5: Non-compliance can lead to product recalls, legal penalties, reputational damage, and market bans.