Pain Relief Gel Patches OEM: Building Trust with Quality Assurance
In the increasingly competitive and regulation-driven market of topical pain relief solutions, quality assurance (QA) is not just a regulatory requirement—it’s a powerful trust-building mechanism. Whether you’re working with a Pain Relief Gel Patches Manufacturer to develop a new line of Custom Pain Relief Gel Patches or launching Private Label Pain Relief Gel Patches, one thing remains essential: quality assurance must be the backbone of your OEM partnership.
This article delves into how Pain Relief Gel Patches OEM partners can ensure consistent quality, regulatory compliance, and consumer trust—and why these elements are non-negotiable for success in today’s health and wellness industry.
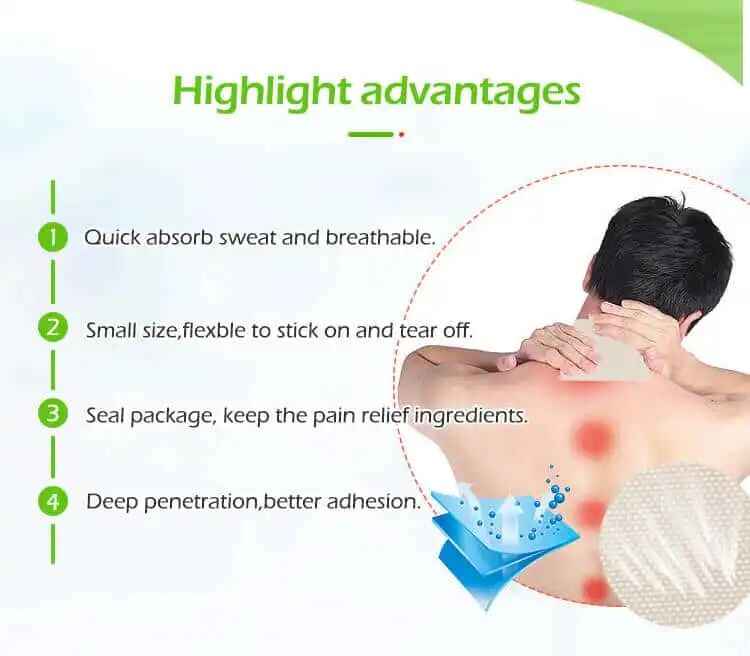
1. Why Quality Assurance Matters in Pain Relief Gel Patches OEM
Trust Starts with Quality
Consumers rely on pain relief patches to ease discomfort, reduce inflammation, and enhance mobility. If a patch is ineffective—or worse, causes adverse reactions—it erodes consumer trust instantly.
A rigorous quality assurance system ensures that every patch:
Delivers the promised relief consistently
Contains only safe, tested ingredients
Meets local and international safety standards
Maintains integrity throughout its shelf life
With consumer expectations rising and competition growing, QA becomes a critical brand differentiator.
2. The Role of the OEM in Ensuring Quality
What a Reliable Pain Relief Gel Patches OEM Should Offer:
A trustworthy Pain Relief Gel Patches OEM doesn’t just manufacture. It becomes a strategic partner in quality management. Look for these capabilities:
GMP-Certified Facilities: Good Manufacturing Practices ensure safety, hygiene, and precision.
ISO Certifications (e.g., ISO 13485): Indicate adherence to medical device manufacturing standards.
Raw Material Traceability: Full documentation of sourcing and safety of all components.
In-House Quality Control (QC) Teams: For ongoing batch testing and product validation.
Regulatory Compliance Support: Helps your products meet FDA, CE, or TGA requirements.
3. Key Components of a Strong Quality Assurance Program
To build consumer trust and maintain brand credibility, your Pain Relief Gel Patches Supplier must uphold several pillars of QA:
A. Ingredient Quality and Transparency
Each active and inactive ingredient must be:
Verified for purity and potency
Sourced from reputable suppliers
Accompanied by Certificates of Analysis (CoAs)
Ingredients like menthol, capsaicin, CBD, or herbal extracts must meet safety thresholds.
Especially for Custom Pain Relief Gel Patches, ingredient selection must balance innovation with tested efficacy.
B. Formulation Consistency
Uniform blending techniques ensure that the active ingredients are evenly distributed.
Patch thickness, gel viscosity, and absorption rate should remain consistent from batch to batch.
This is especially critical for Private Label Pain Relief Gel Patches, where product performance reflects directly on your brand.
C. Packaging Integrity
Protective, tamper-proof, and moisture-resistant packaging helps maintain product quality.
All labels must display required information: ingredients, batch number, manufacturing/expiry dates, and usage directions.
A QA-compliant Pain Relief Gel Patches Manufacturer will validate that packaging preserves both function and compliance.
D. Shelf Life and Stability Testing
OEMs must conduct real-time and accelerated stability studies to ensure that your patch remains safe and effective until its expiration.
Packaging and environmental exposure (heat, humidity) are evaluated over time.
4. Regulatory Compliance as Part of Quality Assurance
Compliance isn’t just a legal obligation—it’s a signal of quality to your customers. A strong Pain Relief Gel Patches OEM must navigate and align with:
FDA regulations in the U.S. (e.g., 21 CFR 210/211 for drug products)
EU MDR regulations for medical devices with CE marking
TGA compliance in Australia
NMPA approval for the Chinese market
Global-ready Pain Relief Gel Patches Suppliers maintain updated regulatory knowledge and guide their clients through:
Product registration and labeling
Ingredient documentation
Technical dossiers for market entry
GMP audit preparations
5. How Quality Assurance Builds Brand Trust and Market Longevity
A. Fewer Product Recalls
With a robust QA system, the risk of product recalls is significantly reduced—safeguarding your brand reputation and minimizing financial losses.
B. Stronger Consumer Loyalty
End-users quickly notice and appreciate consistent product quality. A pain patch that works well every time earns repeat purchases and word-of-mouth marketing.
C. Positive Brand Perception
Private label products manufactured with a high QA standard often outperform name brands because consumers view them as premium and reliable.
D. Easier Market Expansion
A consistent QA record makes international expansion smoother, as distributors, retailers, and regulators are more likely to trust your brand.
6. Questions to Ask Your Pain Relief Gel Patches OEM Partner
Before entering into a contract with a Pain Relief Gel Patches Manufacturer, ask the following:
Are your facilities GMP and ISO certified?
What in-process and final product testing do you conduct?
Do you provide full batch documentation and CoAs?
Can you support regulatory registration for multiple countries?
How do you handle quality deviations or complaints?
The answers to these questions help determine if your OEM is ready to deliver consistent quality at scale.
7. Building a Customized QA Framework for Your Brand
If you’re developing Custom Pain Relief Gel Patches, you can collaborate with your OEM to build a customized QA protocol, including:
Tailored QC checkpoints for your unique formula
Third-party testing for allergen screening, heavy metals, and microbiological safety
Customized packaging testing (e.g., UV resistance, adhesive performance)
Pilot production runs to evaluate quality before full-scale launch
This process ensures that your product reflects your brand promise and exceeds consumer expectations.
8. Common Quality Assurance Challenges—and How to Solve Them
Challenge | Solution |
---|---|
Ingredient variability between suppliers | Work with a Pain Relief Gel Patches Supplier that ensures batch testing |
Packaging failure during distribution | Perform accelerated shipping simulations |
Inconsistent patch adhesion | Adjust formulation and test across multiple skin types |
Difficulty in regulatory approval | Choose an OEM with global compliance expertise |
9. Case Study: QA Excellence in Action
Brand Profile: A startup brand in the sports wellness space launched Private Label Pain Relief Gel Patches aimed at athletes.
OEM Strategy:
OEM conducted independent patch efficacy testing.
Implemented triple-layer packaging for moisture and tamper resistance.
Supplied detailed CoAs for all ingredients and patches.
Supported the brand through FDA OTC monograph compliance.
Result: 97% customer satisfaction in post-purchase surveys and acceptance by two major retail chains within 6 months.
Conclusion: Choose Quality First, Build Trust Always
In the world of Pain Relief Gel Patches OEM, quality assurance is more than a technical necessity—it’s a strategic brand asset. Whether you're producing Custom Pain Relief Gel Patches or scaling with Private Label Pain Relief Gel Patches, consumers want products they can trust.
And trust isn’t given—it’s earned through every batch, every test, and every satisfied customer. By working with a qualified Pain Relief Gel Patches Manufacturer and building a robust QA system, your brand can not only meet market demands but lead with integrity and long-term impact.
FAQs: Quality Assurance in Pain Relief Gel Patches OEM
Q1: What is the role of QA in Pain Relief Gel Patches OEM?
A1: QA ensures the safety, consistency, and efficacy of every patch manufactured—building consumer trust and brand credibility.
Q2: How do I verify that a Pain Relief Gel Patches Manufacturer has good QA practices?
A2: Look for GMP/ISO certifications, ask about testing protocols, and request documentation such as CoAs and stability data.
Q3: Is QA important for Private Label Pain Relief Gel Patches?
A3: Absolutely. QA protects your brand image, ensures legal compliance, and enhances customer satisfaction.
Q4: Can I customize QA protocols for my Custom Pain Relief Gel Patches?
A4: Yes. A good OEM partner will collaborate with you to tailor QA checkpoints to your unique formula and branding needs.
Q5: What regulatory standards must be met for pain relief patches?
A5: Standards vary by country but often include FDA (USA), CE (Europe), TGA (Australia), and NMPA (China). Your OEM should guide you through this.