How Long Does the Customization Process Take for Custom Heat Therapy Patches?
The customization process for Custom Heat Therapy Patches can vary greatly depending on several factors, including the complexity of the design, the type of customization required, and the capabilities of the Heat Therapy Patch Manufacturer. Whether you are looking to develop a Private Label Heat Therapy Patch or seeking to collaborate with a Heat Therapy Patch OEM for more tailored products, understanding the timeline for customization is crucial for effective planning. This article will explore the typical steps involved in the customization process and offer insights into how long it takes to create your ideal Custom Heat Therapy Patch.
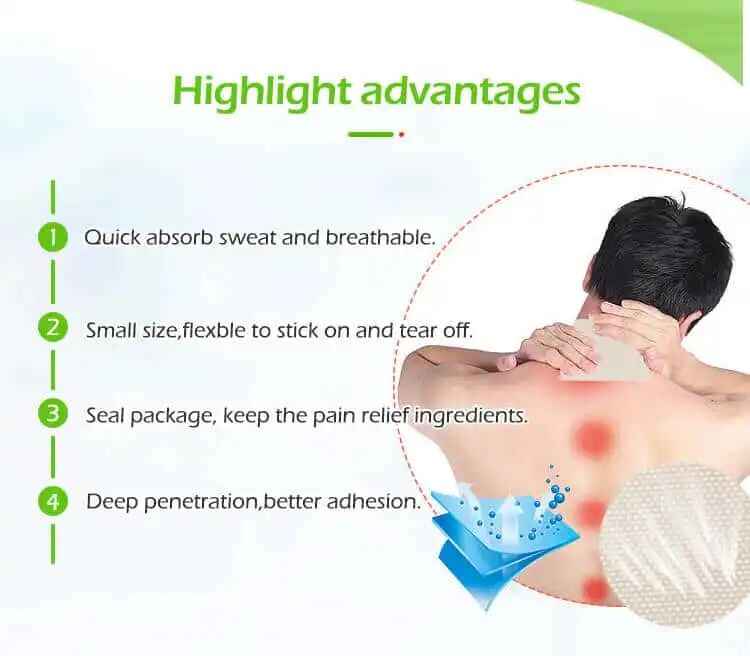
1. Initial Consultation and Requirements Gathering
The first step in customizing a Heat Therapy Patch is to meet with the manufacturer and define the specifications for your product. This includes deciding on the ingredients, design, size, and packaging for the patch.
Key Decisions: When working with a Heat Therapy Patch Manufacturer, you will need to discuss critical factors such as:
Type of heat source (e.g., activated by air, body temperature, etc.)
Active ingredients (e.g., menthol, capsaicin, essential oils)
Patch size and shape
Packaging and labeling
Compliance with local or international regulations
Timeline: This initial stage usually takes between 1 to 2 weeks. It’s a critical phase because the manufacturer needs to understand your exact requirements to provide an accurate quote and timeline.
2. Prototyping and Sample Development
Once the specifications are agreed upon, the next step is the creation of a prototype. The manufacturer will design a sample Custom Heat Therapy Patch that meets your requirements. This sample allows you to evaluate the product before committing to mass production.
Prototype Details: The manufacturer will produce a prototype that includes the following:
The heating element that meets your therapeutic needs.
The patch material (e.g., fabric, non-woven material).
The adhesive and protective layers that ensure the patch stays in place during use.
Packaging samples that reflect your brand and design preferences.
Timeline: Creating and testing a prototype typically takes 2 to 4 weeks. Depending on the complexity of the product and any design revisions, this timeline can vary. Be prepared for possible back-and-forth communication to fine-tune the prototype.
3. Testing and Quality Assurance
Once the prototype is ready, it must undergo a series of tests to ensure its effectiveness, safety, and compliance with health and safety standards. This is an essential step, particularly for Private Label Heat Therapy Patches and Custom Heat Therapy Patches, as these products often require regulatory approvals.
Key Tests:
Performance Testing: Ensures that the patch heats effectively and provides the intended therapeutic benefits.
Safety Testing: Ensures that the patch is safe for use on the skin and adheres to all relevant health standards.
Shelf Life Testing: Determines how long the patch remains effective and safe to use.
Packaging Integrity: Ensures that the packaging maintains the patch's quality and functionality during transportation and storage.
Timeline: Testing and quality assurance can take 2 to 4 weeks, depending on the complexity of the tests required and any necessary adjustments to the formulation or design.
4. Finalizing the Design and Approval
Once the prototype has been tested and approved, the next step is to finalize the design and confirm any final adjustments to the product. This is when the manufacturer will ensure that everything is aligned with your brand's specifications before beginning mass production.
Approval Process: This phase typically involves a review of the final product sample, packaging design, and any necessary documentation (e.g., certifications, labels). It's important to verify that the product meets all your expectations regarding quality, branding, and functionality.
Timeline: Finalizing the design and obtaining approval can take anywhere from 1 to 2 weeks. During this phase, your feedback is crucial to ensure that the Custom Heat Therapy Patch matches your vision and branding.
5. Mass Production and Delivery
Once the final design is approved, the manufacturer will begin mass production of your Custom Heat Therapy Patches. During this phase, the manufacturer will produce the required quantities of the patches and prepare them for delivery.
Production Process: This involves setting up the production lines, sourcing raw materials, manufacturing the patches, packaging, and labeling the product. Some manufacturers, particularly those offering Heat Therapy Patch OEM services, may handle all of these elements in-house.
Timeline: The production phase typically takes 3 to 6 weeks, depending on the order size and the manufacturer's production capacity. This phase can be faster if the manufacturer has pre-existing materials and a streamlined production process. Delivery time may vary depending on your location and shipping methods.
6. Total Customization Time
Taking all the stages into account, the entire process of customizing Heat Therapy Patches, from the initial consultation to mass production, usually takes between 8 to 12 weeks. However, this timeline can vary depending on the complexity of the customization, the responsiveness of both parties, and the scale of the production order.
Factors That Affect Customization Time:
Product Complexity: More intricate patches with multiple active ingredients, special features (e.g., multi-layer patches), or unique packaging may require additional time to develop.
Regulatory Approval: If your patches are intended for medical use or need to meet specific regulatory standards, the approval process could add time to the overall timeline.
Order Size: Larger orders may take more time to produce, while smaller orders might be completed more quickly.
Frequently Asked Questions (FAQs)
What is the first step in customizing a Heat Therapy Patch?
The first step is a consultation with a Heat Therapy Patch Manufacturer to define your product’s specifications, including ingredients, design, and packaging.
How long does it take to get a prototype of a Custom Heat Therapy Patch?
Creating a prototype typically takes 2 to 4 weeks, depending on the complexity of the product.
Are there any tests required for Custom Heat Therapy Patches?
Yes, Custom Heat Therapy Patches must undergo performance, safety, and shelf-life testing to ensure the product is effective and compliant with health regulations.
How long does the mass production of Heat Therapy Patches take?
Mass production typically takes 3 to 6 weeks, depending on the order size and production capabilities of the manufacturer.
Can the customization process for Private Label Heat Therapy Patches be faster?
Yes, Private Label Heat Therapy Patches often have a quicker turnaround because the formula and packaging are pre-designed by the manufacturer, leaving only customization of branding and packaging.
What affects the timeline of customizing a Heat Therapy Patch?
The complexity of the product, regulatory approvals, and order size can all impact the timeline for Custom Heat Therapy Patches.
Conclusion
The customization process for Custom Heat Therapy Patches typically takes between 8 to 12 weeks, depending on various factors such as product complexity, regulatory requirements, and production scale. By working with an experienced Heat Therapy Patch Manufacturer or Heat Therapy Patch OEM, you can ensure that your product is developed efficiently, meets all necessary standards, and is ready for launch in a reasonable timeframe. Understanding the stages of customization and the timeframes involved allows you to plan effectively and bring your heat therapy product to market with confidence. Whether you’re looking to create a Private Label Heat Therapy Patch or a highly customized solution, the right manufacturer can make the process smoother and faster.