How Long Does It Take to Produce Custom Cold Therapy Patches?
When planning to launch Custom Cold Therapy Patches under your brand, understanding the production timeline is critical. Whether you are working with a Cold Therapy Patches Manufacturer, a Cold Therapy Patches OEM, or a Cold Therapy Patches Supplier, realistic expectations about production lead time will help you better plan your inventory, marketing, and product launches.
In this comprehensive guide, we’ll break down each stage of the production process for Private Label Cold Therapy Patches, explain the factors that impact timelines, and provide best practices to speed up production without compromising quality.
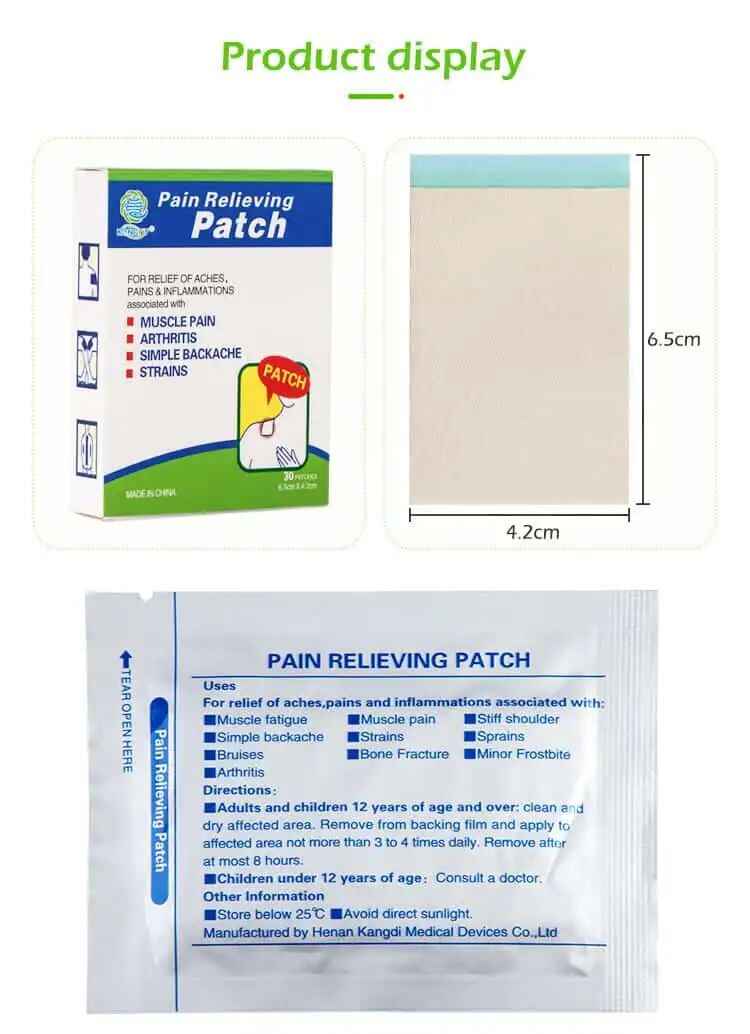
1. Typical Timeline for Producing Custom Cold Therapy Patches
The full process from initial inquiry to delivery of finished Custom Cold Therapy Patches generally takes between 8 to 16 weeks. The timeline can be broken down into the following stages:
Stage | Estimated Duration |
---|---|
Initial consultation & requirement gathering | 1–2 weeks |
Formulation development & sampling | 3–5 weeks |
Sample testing and approval | 1–2 weeks |
Mass production preparation | 1 week |
Manufacturing and quality assurance | 3–6 weeks |
Packaging and final inspections | 1–2 weeks |
Shipping and logistics | Depending on destination (1–4 weeks) |
Each phase plays a critical role in ensuring that your Private Label Cold Therapy Patches meet your brand’s quality standards and regulatory requirements.
2. Key Factors That Influence Production Time
Several factors can either shorten or extend the production cycle when dealing with a Cold Therapy Patches Manufacturer or Cold Therapy Patches OEM:
a. Complexity of Customization
Simple adjustments, like adding a brand logo or minor ingredient tweaks, can move quickly. However, creating entirely new formulations, especially those involving special ingredients (e.g., organic components, CBD infusions), requires extensive R&D and testing.
b. R&D Capabilities
A Cold Therapy Patches Supplier with strong in-house R&D will typically shorten development cycles, thanks to established processes, ingredient libraries, and expertise.
c. Regulatory Requirements
If your Custom Cold Therapy Patches need to comply with regulations like FDA, CE marking, or other regional certifications, the timeline may extend due to stability studies, clinical testing, or additional documentation.
d. Order Quantity
Larger batch sizes usually require more production time. However, reputable Cold Therapy Patches Manufacturers often have scalable production lines to handle bulk orders efficiently.
e. Material Availability
Sourcing rare or specialty ingredients or materials can delay production. Early confirmation of all materials needed is critical.
f. Seasonal Demand
During peak seasons (e.g., winter flu season, summer sports injuries), Cold Therapy Patches Suppliers may have longer queues. Planning production well ahead is crucial during these times.
3. Detailed Breakdown of the Production Process
Let’s dive deeper into each step:
a. Initial Consultation
You and the Cold Therapy Patches Manufacturer discuss your brand goals, product specifications, target market, and any required certifications. Clear communication at this stage ensures fewer revisions later.
b. Formulation Development
For Custom Cold Therapy Patches, the R&D team designs the patch's hydrogel base, cooling ingredients, adhesive properties, and additional functional additives if needed.
c. Sampling and Testing
The OEM produces lab-scale samples for your review. It's essential to evaluate cooling efficacy, skin feel, adhesive strength, and allergen response.
d. Approval Process
After feedback and possible minor adjustments, you officially approve the final formula and design for mass production.
e. Mass Production Preparation
Includes ordering raw materials, setting up production schedules, and quality control prechecks.
f. Manufacturing
This phase covers:
Hydrogel preparation
Sheet forming and cutting
Application of adhesives
Primary packaging into individual sachets or pouches
g. Quality Assurance
Before packing, QA teams perform:
Adhesion strength tests
Cooling duration tests
Microbial limit tests
Stability testing (as needed)
h. Packaging
Branded packaging is printed, assembled, and filled. The Cold Therapy Patches Supplier may also conduct final product inspections before shipping.
4. How to Speed Up Custom Cold Therapy Patch Production
a. Choose a Full-Service Cold Therapy Patches OEM
Working with a one-stop Cold Therapy Patches Manufacturer that handles R&D, production, and packaging under one roof saves significant time.
b. Provide Clear Specifications Upfront
The more detailed your initial brief (desired ingredients, patch size, packaging preferences), the fewer revisions will be necessary.
c. Pre-approve Common Materials
If possible, select from the supplier's existing raw material library to skip lengthy sourcing times.
d. Plan for Parallel Processes
Start packaging design and regulatory paperwork while the product formulation is being finalized.
5. The Importance of Realistic Timelines
Rushing the production of Private Label Cold Therapy Patches can lead to:
Poor product performance (e.g., patches that fall off easily)
Regulatory non-compliance
Damaged brand reputation
Increased costs from rework or recalls
Allowing sufficient time ensures thorough testing, proper documentation, and high-quality final products that align with your brand’s promise.
6. Real-World Example: A Success Story
A U.S.-based sports recovery brand worked with a Cold Therapy Patches Supplier to launch a line of CBD-infused cooling patches. Thanks to early and clear communication, leveraging the supplier’s existing ingredient databases, and concurrent packaging development, the company brought their Custom Cold Therapy Patches to market in just 10 weeks, two weeks faster than the industry average.
By choosing a Cold Therapy Patches OEM with robust R&D, in-house manufacturing, and flexible production schedules, they successfully timed their launch with peak sports season, boosting sales dramatically.
Conclusion: Plan Smart, Partner Wisely
Producing Custom Cold Therapy Patches typically takes 8–16 weeks, depending on complexity, customization, and regulatory demands. Choosing a reputable, full-service Cold Therapy Patches Manufacturer or Cold Therapy Patches OEM is key to ensuring a smooth, efficient production process.
By understanding each stage, planning ahead, and maintaining clear communication with your Cold Therapy Patches Supplier, you can minimize delays and launch high-quality Private Label Cold Therapy Patches that strengthen your brand's position in the marketplace.
Related Questions & Answers
Q1: Can a Cold Therapy Patches OEM accelerate production for urgent projects?
A: Yes, some suppliers offer expedited services for an additional fee, but quality and compliance must not be compromised.
Q2: What is the minimum production time for simple Private Label Cold Therapy Patches?
A: For straightforward designs using existing formulas, production can be completed in as little as 6–8 weeks.
Q3: How can I ensure faster approval of samples?
A: Provide prompt, detailed feedback on sample tests and be decisive about minor adjustments.
Q4: Are there seasonal factors that affect Cold Therapy Patches production timelines?
A: Yes, production lines may be busier during health and sports seasons. Early booking is recommended.
Q5: Does using custom ingredients significantly slow down production?
A: It can. Custom ingredients may require sourcing, safety validation, and stability testing, all of which add time.