Herbal Capsicum Patches OEM Quality Control: How to Ensure Product Safety and Efficacy
In the competitive and highly regulated herbal pain relief market, quality control is not just a regulatory requirement—it’s a critical factor in brand trust and long-term success. Whether you're working with a Herbal Capsicum Patches Manufacturer to develop a new product line or expanding your existing offering through Private Label Herbal Capsicum Patches, ensuring safety and efficacy must be at the core of your OEM strategy.
This article provides a comprehensive and SEO-optimized guide to understanding and managing quality control in the Herbal Capsicum Patches OEM process. We'll explore best practices, manufacturing standards, testing protocols, and how to choose the right Herbal Capsicum Patches Supplier for a secure and effective product.
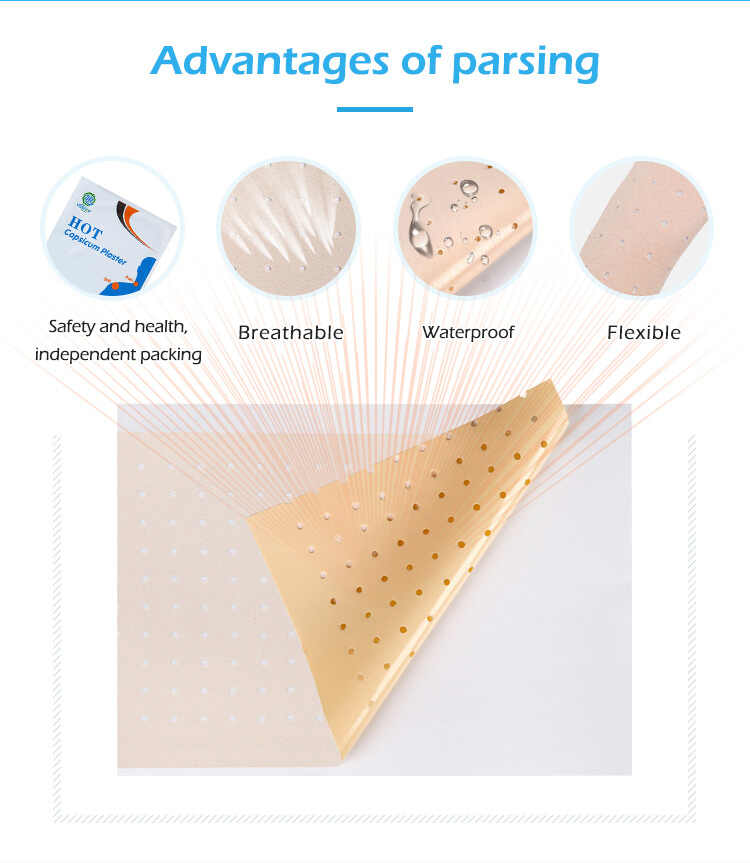
1. Why Quality Control Matters in Herbal Capsicum Patches OEM
Consumers today expect not only natural ingredients but also clinically proven, consistently effective, and safe-to-use products. With Herbal Capsicum Patches, where active ingredients like capsaicin are absorbed through the skin, quality assurance becomes especially crucial.
Without rigorous quality control:
Product efficacy may vary across batches
Unsafe levels of active compounds may cause irritation
The brand risks regulatory penalties or product recalls
That's why a reliable Herbal Capsicum Patches Manufacturer must adopt a quality-first approach in both formulation and production.
2. Key Quality Control Areas in Herbal Capsicum Patches OEM
To ensure the safety and efficacy of Custom Herbal Capsicum Patches, manufacturers and brand owners must control quality in the following areas:
a. Raw Material Selection and Testing
Use high-grade herbal extracts, especially capsaicin, menthol, and camphor.
Require Certificates of Analysis (COA) from ingredient suppliers.
Test for contaminants: pesticides, heavy metals, microbial load.
b. Formulation Consistency
Maintain precise concentration levels of active ingredients to ensure therapeutic consistency.
Stability testing under various temperature and humidity conditions.
Use validated emulsifiers and adhesives to ensure consistent absorption through the skin.
c. Patch Adhesion and Delivery Mechanism
Conduct adhesion tests to measure patch stickiness and wear duration.
Ensure even distribution of active ingredients across the patch surface.
Verify the release profile matches desired therapeutic outcomes (e.g., 8-hour relief).
d. Microbiological Safety
Implement GMP-compliant cleanroom conditions.
Conduct batch testing for bacterial and fungal contamination.
Use appropriate preservatives to maintain shelf life.
e. Packaging Integrity
Use airtight, moisture-resistant materials to preserve patch effectiveness.
Perform leak and stability tests.
Include lot numbers and expiration dates for traceability.
3. Certifications to Look For in a Herbal Capsicum Patches Manufacturer
Before selecting a Herbal Capsicum Patches OEM, verify their certifications. This indicates adherence to international standards in manufacturing, safety, and product testing.
Essential certifications:
GMP (Good Manufacturing Practices) – ensures cleanliness and consistency
ISO 13485 – applicable for medical device-grade patches
FDA Registration (US Market) – required for OTC patches
CE Marking (EU Market) – required if classified as a medical device
ISO 22716 – cosmetic GMP standard, especially for wellness products
A Herbal Capsicum Patches Supplier with these credentials will help you avoid regulatory roadblocks and build consumer trust.
4. In-Process Quality Control for OEM Production
A well-established Herbal Capsicum Patches OEM will have an internal quality assurance (QA) and quality control (QC) team monitoring the entire production cycle.
Common checkpoints:
Ingredient weighing accuracy
Batch uniformity verification
Patch cutting precision
Label accuracy check
Packaging sealing and printing inspection
Each stage is tracked and logged for compliance and traceability.
5. Post-Production Testing: Ensuring Product Efficacy
After manufacturing, Custom Herbal Capsicum Patches must undergo a series of post-production evaluations to verify performance.
Standard post-production tests include:
Skin irritation and sensitization tests on volunteers or synthetic skin models
Efficacy validation through small-scale clinical or observational trials
Shelf-life simulation under accelerated aging conditions
Tensile and peel strength testing for user comfort and adhesion
These tests ensure the patches deliver consistent relief while minimizing adverse skin reactions.
6. Documentation and Traceability: Minimizing Risk
Your Herbal Capsicum Patches Supplier should provide complete documentation for each batch to help with audits, recalls, and regulatory submissions.
Critical documents:
COA (Certificate of Analysis)
MSDS (Material Safety Data Sheets)
Batch Manufacturing Records
Stability Test Reports
Product Safety Reports (EU)
FDA Establishment Registration (US)
Strong documentation ensures product transparency, legal protection, and faster international approvals.
7. Custom Herbal Capsicum Patches and Risk Management
Creating Custom Herbal Capsicum Patches requires extra attention to quality because unique combinations of herbs, oils, and adhesives may introduce unexpected interactions or skin responses.
How to manage risk:
Begin with small-scale batch trials
Conduct compatibility testing of new herbal ingredients
Use dermatologically tested adhesives
Set up a post-market surveillance system to gather consumer feedback
An experienced Herbal Capsicum Patches OEM will guide you through these steps efficiently.
8. Private Label Herbal Capsicum Patches: Trusting Proven Formulations
Opting for Private Label Herbal Capsicum Patches gives you the benefit of using already validated and tested formulas, which significantly reduces development and regulatory time.
Advantages:
Proven stability and performance
Pre-approved safety documentation
Faster launch with consistent quality
Choose an OEM who offers white-label solutions with built-in quality assurance protocols. These are ideal for health brands that want speed-to-market without compromising safety.
9. Red Flags to Avoid When Selecting an OEM
Not every Herbal Capsicum Patches Manufacturer upholds the same standards. Beware of the following:
❌ No GMP or ISO certifications
❌ Incomplete ingredient transparency
❌ No third-party lab testing offered
❌ Inability to provide batch-level documentation
❌ Slow response or vague answers to compliance questions
Always request quality audit reports or a virtual tour of the production facility before committing to any Herbal Capsicum Patches OEM partner.
10. Final Thoughts: Building Consumer Confidence Through Quality
To stand out in the herbal wellness market, you must prioritize quality at every stage of the Herbal Capsicum Patches OEM process. From raw materials to finished product testing, each element contributes to user safety, product performance, and regulatory approval.
By partnering with a certified and experienced Herbal Capsicum Patches Supplier, you can deliver high-quality products that earn consumer trust and regulatory acceptance across global markets.
Whether you choose Custom Herbal Capsicum Patches or a Private Label Herbal Capsicum Patches solution, rigorous quality control is your strongest competitive advantage.
Related Questions and Answers
Q1: What certifications should a Herbal Capsicum Patches Manufacturer have?
A1: Look for GMP, ISO 13485 or 22716, FDA registration, and CE marking for international credibility.
Q2: How do OEMs ensure product safety in Herbal Capsicum Patches?
A2: Through microbiological testing, dermatological safety trials, and batch-specific documentation.
Q3: Can I still ensure high quality if I choose Private Label Herbal Capsicum Patches?
A3: Yes, reputable OEMs use pre-tested, stable formulations that come with full safety documentation.
Q4: What tests verify Herbal Capsicum Patch efficacy?
A4: Skin absorption studies, stability tests, release rate evaluations, and user trials.
Q5: How do I confirm a Herbal Capsicum Patches Supplier is compliant?
A5: Ask for audit records, third-party lab results, and detailed manufacturing SOPs.